Ever wonder how stuff actually gets from an online store to your front door, sometimes in less than 24 hours? It’s not just magic or armies of delivery vans—there’s a whole digital system working in the background. At the heart of it is logistics software, quietly organizing thousands of moving parts so your package lands exactly where you want it.
Picture this: You click "Buy Now" on a website. Immediately, a logistics system kicks in to figure out which warehouse has your item, checks its stock, tells workers to pick and pack it, and sets up a delivery route for the driver. Every bit of this is tracked, updated, and relayed using software that connects warehouses, trucks, drivers, and even you via tracking links.
This article isn’t just about theory—you’ll see exactly how a typical logistics system works, where all the tech comes into play, and how companies keep errors and delays at a minimum. Let's get into the nuts and bolts of a real-world logistics setup.
- What Makes Up a Logistics System?
- Software as the Brain Behind Logistics
- A Day in the Life: From Order to Delivery
- Why Good Logistics Software Matters
- Tips for Picking the Right Solution
What Makes Up a Logistics System?
A logistics system isn’t just about moving boxes; it pulls together people, software, and tools so everything moves smoothly from start to finish. Think of it like a puzzle, where each piece plays a specific role.
The main chunks that keep the whole thing running are:
- Inventory Management: This is where the system checks what’s in stock, updates quantities as items move in and out, and alerts workers if something’s running low. Real-time updates here are key to avoid overselling or lost sales.
- Warehouse Management: Here’s where the software gives packing teams exact aisle locations, directs them to the right shelves, and makes sure nothing gets misplaced. Modern systems often use barcodes or even robots to speed things up.
- Order Processing: Once someone buys something, the system creates a digital order, grabs the right products, and preps it for packing and shipping. Mistakes here can mean unhappy customers or extra costs.
- Transportation Management: This covers route planning for trucks, handling delivery schedules, and syncing with drivers’ devices. Routing software here actually cuts down delivery times and fuel costs.
- Delivery Tracking: From the second a package leaves the warehouse, tracking features share live status updates with customers and support teams. Delivery tracking apps have become expected—folks like seeing that real-time "out for delivery" ping!
You might be surprised, but a 2023 survey found that 65% of logistics companies said end-to-end logistics software saves them at least 10 hours per week per employee compared to manual processes. That adds up fast, especially at scale.
System Element | Main Function |
---|---|
Inventory Management | Real-time stock visibility |
Warehouse Management | Efficient item picking/packing |
Order Processing | Accurate order fulfillment |
Transportation Management | Optimized delivery routes |
Delivery Tracking | Live updates for customers |
When you piece these elements together—all with smart logistics software as the backbone—you’ve got a setup that can handle whatever gets thrown at it, from Black Friday spikes to last-minute delivery changes. That’s what keeps the modern supply chain humming.
Software as the Brain Behind Logistics
If you peek behind the scenes of any top-tier logistics system, you'll find software calling the shots. This isn't just for planning routes or updating inventory—modern logistics software is what keeps the whole supply chain glued together, even in fast-moving, high-stress situations like Black Friday or holiday rushes.
This software pulls real-time info from a bunch of sources: warehouse scanners, inventory databases, GPS trackers on delivery trucks, and even your tracking clicks. All of that data gets processed and handed back out as clear instructions. Workers see exactly which shelf to grab a product from. Drivers get the fastest routes, with live traffic updates. Managers see which orders are lagging and why. And you get that "Your package is on the way" update almost instantly.
One popular type of logistics software is called a warehouse management system (WMS). A solid WMS will monitor stock levels by the minute, flag low inventory, and coordinate with order processing tools. Some systems can even predict which products are about to run out based on shopping trends from sources like Shopify or Amazon.
On the transport side, you’ve got transportation management systems (TMS). These tools map out delivery routes, optimize loads, track fuel usage, and send out alerts if a truck gets delayed or lost. Companies like FedEx and UPS rely on huge, custom logistics databases to decide—literally in seconds—where to ship items from and how to pack each truck for max efficiency.
Here’s a real kicker: the global logistics software market hit nearly $11 billion last year, and it’s growing every year. Why? Because so many businesses now count on logistics software to avoid expensive mistakes and keep up with customer expectations.
Feature | Impact |
---|---|
Automated order processing | Speeds up shipments, cuts errors |
Real-time tracking | Keeps customers and staff in the loop |
Inventory forecasting | Reduces out-of-stocks |
Route optimization | Saves fuel and labor costs |
Bottom line: without powerful, connected software running the show, today’s rapid delivery tracking and perfectly timed shipments wouldn’t be possible.
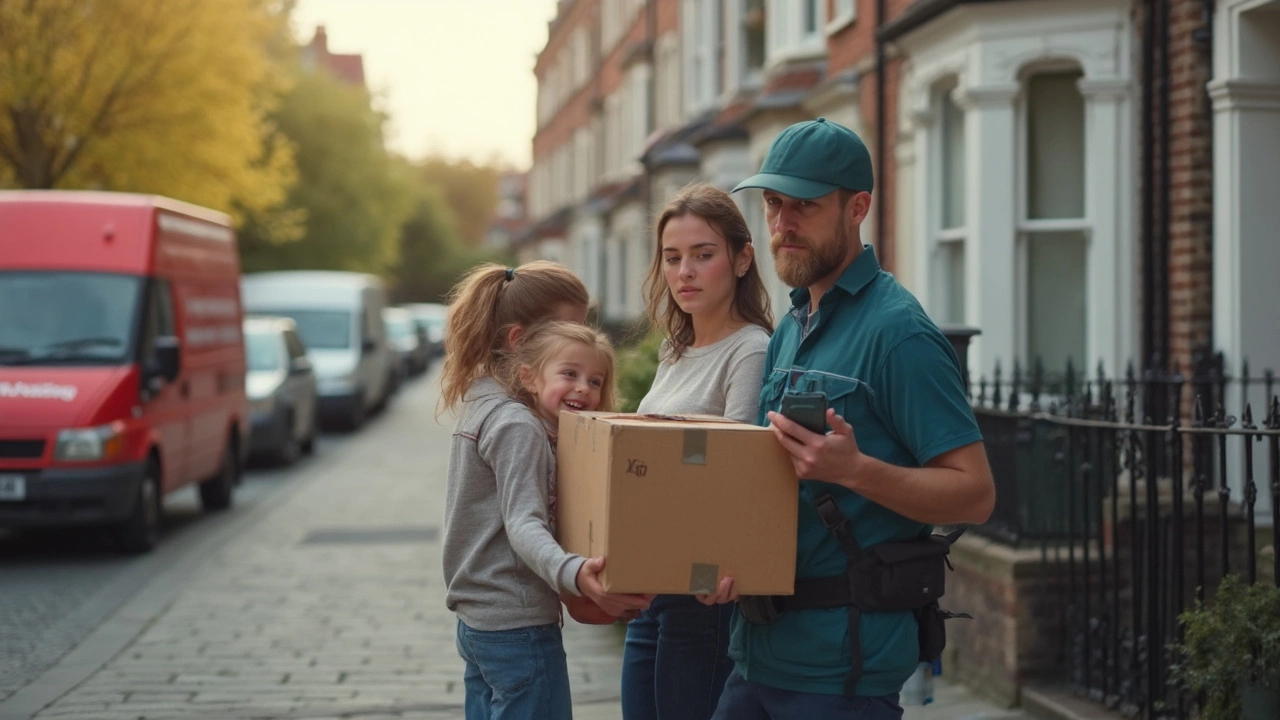
A Day in the Life: From Order to Delivery
Let’s walk through exactly what happens after you hit that checkout button. Modern logistics system software is all about speed and accuracy, and here’s how it works, step by step.
- Order placed: The system scans available inventory across connected warehouses. If your item is in stock, it reserves it instantly so nobody else can snag it.
- Warehouse alert: Warehouse workers get a notification to pick and pack your item. Software assigns tasks based on who is closest, or who’s got free hands. Fun fact: Big operations like Amazon use robotics to bring shelves to workers, but even smaller operations rely on strong logistics software to avoid mix-ups.
- Shipping decision: The system chooses the best shipping route and carrier based on price, location, and how fast you want your stuff. It can even auto-generate shipping labels and predict when your package will arrive.
- Out for delivery: Vehicles are loaded in a specific order, streamlining drop-offs. Drivers use GPS-powered apps linked to the logistics software for real-time updates and route changes in case of traffic or delays.
- Delivery tracking: Throughout the journey, you get notifications: packed, shipped, out for delivery. Every update comes from that same backend software, so you’re never guessing where your stuff is.
Here’s how this typically plays out in numbers for a busy e-commerce warehouse:
Step | Time Taken (Avg) |
---|---|
Order Processed | 30 seconds |
Picking & Packing | 7 minutes |
Shipping Label Generated | 15 seconds |
Last Mile Delivery | 2-24 hours |
All these moving parts rely on the logistics system talking smoothly to warehouse management, shipment tracking, and delivery apps. That’s why companies invest so heavily in logistics software—they need that real-time data to avoid chaos and keep customers happy.
Why Good Logistics Software Matters
Without reliable logistics software, even the most organized warehouse can turn into a total mess. It doesn’t just schedule deliveries; it slashes mistakes and cuts down on wasted time. For example, a 2023 report from Statista found that companies using advanced logistics systems lowered delivery delays by more than 30% in just one year. That’s huge, especially when speed and accuracy drive customer happiness these days.
Here’s what happens when your software is up to the task:
- Real-time inventory updates: No more guessing what’s on the shelf. As products move in and out, everything stays up to date for both staff and customers.
- Smarter delivery routes: Drivers get the best routes with live traffic data, which means parcels show up faster and with fewer detours.
- Fewer human errors: Automatic data entry and barcode scanning prevent costly mix-ups, like sending the same order twice or shipping to the wrong address.
- Easy tracking: Customers and staff can follow a package’s journey from warehouse to doorstep—no phone calls or endless emails needed.
- Better coordination: Warehouses, delivery vans, and customer service teams all work off the same updated info, so everyone’s on the same page.
Take a look at how companies measure the impact of solid logistics system tools:
Benefit | Before Software | With Software |
---|---|---|
Order Accuracy | 88% | 98% |
Average Delivery Time | 3.5 days | 1.8 days |
Missed Deliveries | 12% | 4% |
All this adds up to happier customers, higher profits, and less stress for teams. If you’re in charge of moving things from A to B, skimping on your logistics software just isn’t worth the risk.
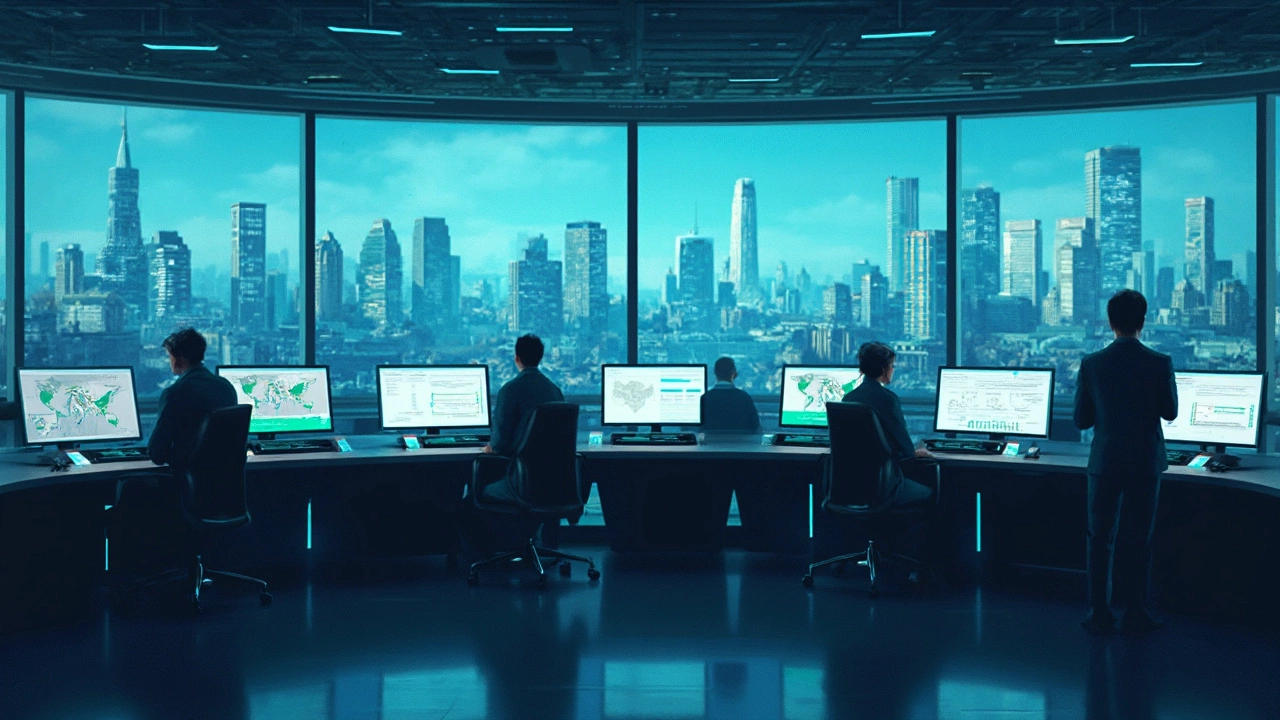
Tips for Picking the Right Solution
Nobody wants a fancy system that just looks good in demos but falls apart in the real world. Picking logistics software is like buying a truck—it’s got to work hard, fit your operation, and actually help your team, not just impress the boss during a pitch. Here’s what you should check before signing on the dotted line.
- Focus on the essentials: Make sure the software covers basics like inventory tracking, order management, and delivery tracking. If you deliver on your own or through third-party shippers, check that it plugs in with their systems. Seamless integration with what you already use is key.
- Cloud vs. on-premises: Cloud-based logistics software saves you from installing servers and lets you scale up as you grow. It also means you’ll get updates automatically and your team can access info wherever they are—pretty handy if folks work remotely or in different time zones.
- User-friendly dashboard: Nobody likes wrestling with clunky software. Look for a dashboard that’s clear and customizable. Try a free demo—ask warehouse or delivery staff to use it for real tasks. If they’re shaking their heads, move on.
- Automation: Chasing down orders, printing pick-lists, or handling returns manually wastes time. Good systems automate repetitive steps. Some even have AI that predicts shipping delays or flags low stock before it becomes a problem.
- Good reporting tools: You’ll need strong reports to spot bottlenecks or see what’s costing you money. Look for software that gives you easy access to data—ideally real-time. If you can’t pull up a report without calling IT, you’ll end up flying blind when problems hit.
- Scalability and support: Can the system grow with you? Ask for examples of companies that started small and scaled up. Also, dig into customer support—do they answer on weekends, or just leave you on hold for hours?
Want a quick peek at what features users care most about? Here’s a breakdown from a 2024 survey of businesses comparing logistics software:
Feature | % of users who rated it as "Very Important" |
---|---|
Real-time delivery tracking | 82% |
Inventory management | 80% |
Ease of integration | 75% |
Automated alerts/notifications | 67% |
Mobile access | 58% |
If you’re unsure where to start, ask logistics staff or drivers what slows them down most. The right logistics system isn’t just a tech upgrade—it’s a tool that helps everyone save time and makes your whole supply chain smoother.