In today's fast-paced world of logistics, choosing the right supply chain software can feel daunting, especially when considering the cost implications. Whether you're a seasoned logistics veteran or just stepping into the realm of supply chain management, understanding the financial landscape of these tools is crucial.
Supply chain software isn't just a tool; it's a backbone that can enhance efficiencies and drive growth. With various pricing models and hidden factors influencing the final cost, it's essential to break down these elements to make an informed decision. From licensing fees to the degree of customization needed, each aspect plays a significant role in shaping how much your chosen software will cost.
- Introduction to Supply Chain Software
- Factors Affecting Software Cost
- Licensing and Subscription Models
- Customization and Integration Costs
- Evaluating ROI and Benefits
Introduction to Supply Chain Software
Imagine the intricacies of moving a product from raw material stage to the final customer. This journey is what the supply chain software aims to simplify. It acts as a critical tool in modern logistics, helping businesses streamline their operations. Its main goal? To create a seamless flow of information and resources, ensuring efficiency and reducing waste at every step of the process.
In a world where speed and precision are king, supply chain software is pivotal. It ensures that everything from manufacturing schedules to inventory levels is in sync. This software equips businesses with real-time data, allowing them to make informed decisions. Imagine getting alerts for stock shortages before they become a problem or optimizing routes for delivery trucks to save on fuel costs. It's not just software; it's a transformative force for competitive advantage.
The evolution of supply chain software can be traced to the need for greater integration in sprawling enterprises. With the rise of global trade and e-commerce, the complexity of supply chains has multiplied. Software solutions have similarly advanced, incorporating artificial intelligence and machine learning to predict demand and improve accuracy. According to a study by Gartner, companies deploying such advanced software reported a 15% increase in operational efficiency.
A diverse array of components makes up supply chain software. This can include procurement solutions, inventory management, logistics, and warehouse management systems, all designed to work in harmony. Each plays a vital role in ensuring the supply chain's health. From tracking the smallest components to monitoring extensive shipping networks, the software provides a central hub from which everything can be coordinated.
Choosing the right supply chain software involves weighing multiple factors. The size of your business, industry specifics, and integration capabilities with existing systems are just a few. The cost of implementation is often determined by these factors as well as the level of customization required. Selecting a robust solution can vastly improve customer satisfaction and revenue growth. As Bill Gates once remarked,
"The advance of technology is based on making it fit in so that you don't really even notice it, so it's part of everyday life." That is exactly the role of supply chain software today.
Supply chain software offers numerous benefits, including enhanced transparency and better communication across networks. This transparency boosts trust between partners and helps in building stronger relationships. Integrating all aspects of the supply chain ensures streamlined communication, reducing the risk of errors and misunderstandings. With increasingly complex supply demands, this integration is invaluable in maintaining quality and efficiency.
Factors Affecting Software Cost
When you're exploring supply chain software, the price tag can sometimes take center stage, and rightly so. But it's not just a number; it's a sum influenced by multiple factors, each playing its part in hitting that bottom line. Let's dive deep into these facets that sway the cost and what you should pay attention to. Understanding these will help businesses make informed choices about their logistics software investments.
Firstly, the type of software significantly affects costs. Whether it’s a cloud-based solution or an on-premises setup, each has its unique set of expenses. Cloud-based services often work on a subscription basis, which might seem lighter on upfront costs but accumulate over time. On the contrary, on-premises systems usually require hefty initial investments due to hardware and long-term maintenance contracts.
Another substantial influencer is the degree of customization and integration required. Off-the-shelf solutions might look tempting with their lower initial costs, but businesses soon find the need to tweak and tailor these tools to fit their unique workflows. Custom integration with existing systems and add-ons for specific functionalities often escalate costs, making it crucial to assess needs carefully upfront.
Licensing Models and User Accounts
The pricing can also fluctuate based on the licensing model. Companies need to decide if they will opt for a perpetual license or a subscription model. Perpetual licenses involve a one-time fee, often with annual maintenance costs, which might be ideal for companies seeking long-term usage. Subscription models, however, offer periodic payments, which can be easier to budget for, though they might end up being pricier in the long run. User accounts further complicate this as additional seats mean additional costs, whether with a one-time license or ongoing subscription fees.
"Choosing the right software isn't just about the features—it’s also about the right spending now to secure savings later," suggests Sarah Johnson, a senior analyst at TechEconomic Review.
Hidden costs such as training for staff and ongoing support should not be overlooked. Staff familiarity with the new system has a learning curve, demanding time and resources. Comprehensive training programs, while necessary, often come at a price. Equally, responsive post-pandemic support is essential, especially in resolving issues swiftly, which can translate to significant costs.
Lastly, geographic location and vendor reputation can have a bearing if not directly, then subtly. Services from reputed vendors or those installed in regions with higher service rates may reflect on the final bill. It’s these nuanced elements that make plotting the exact cost of logistics software somewhat of an art alongside the science.
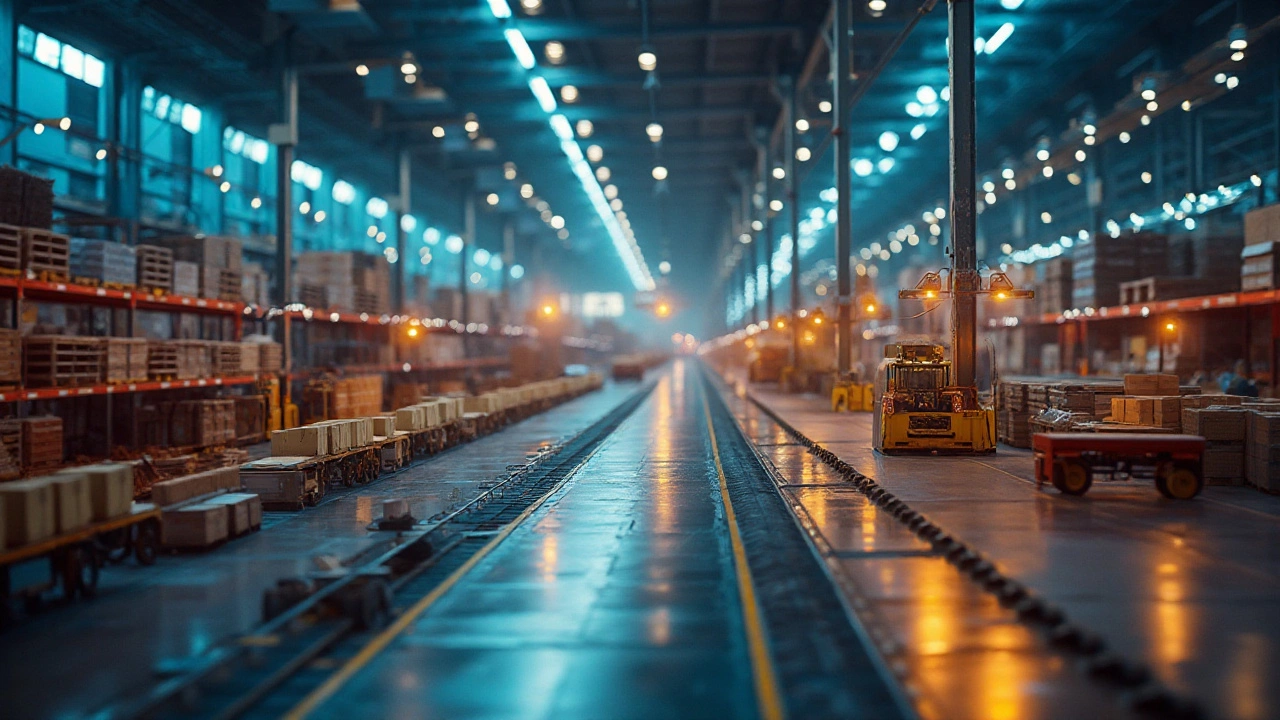
Licensing and Subscription Models
Choosing the right licensing and subscription model for supply chain software is a crucial decision that impacts both short-term budget and long-term growth. In the dynamic world of logistics, flexibility and scalability are often key. Companies should take a close look at whether a one-time licensing fee or an ongoing subscription model best fits their financial goals and operational needs. While a perpetual license might seem attractive with its single upfront cost, it's important to remember the likely ongoing expenses for updates and support. On the other hand, subscription models, often cloud-based, provide regular updates and robust customer support but require continuous payments.
Several factors can influence this decision, including the size of your business, your IT infrastructure, and the frequency of software updates or features required. Large companies with established IT departments might lean towards perpetual licenses, valuing the control and internal management they allow. Small to medium businesses could find the scalability of subscription models particularly beneficial as they grow or adjust to market changes. Logistics software often includes various modules and features, and understanding which of these are bundled into your chosen model can save substantial costs down the line.
It's worth considering that some suppliers offer hybrids that combine elements of both, providing the ownership benefits of a perpetual license with the ongoing feature improvements typical of subscriptions. This flexibility allows companies to tailor their approach to software investment, marrying the best parts of both worlds. In the constantly evolving tech landscape, adaptability can be as critical as efficiency.
According to Gartner, "By 2026, nearly all legacy software products will offer subscription models, recognizing the demand for flexible, scalable solutions in the digital era." This trend highlights the shift in how companies consume software, favoring operating expense models over capital expenditures. For many businesses, having a clear view on total cost of ownership is crucial, as costs can sneak up over time and impact overall profitability.
Finally, when evaluating potential options, businesses should look at case studies or user reviews to gauge the efficacy of each model in scenarios similar to theirs. Cost clarity is essential – a model might appear cost-effective on paper but post-implementation costs, such as user training or system integration, could tip the scales unexpectedly. Understanding how each model aligns with your strategic goals will ensure that your investment in supply chain solutions contributes meaningfully to operational success.
Customization and Integration Costs
Customization and integration play pivotal roles in the adoption of supply chain software, often determining how well a software solution fits within a company's existing operations. A standardized off-the-shelf product might be less costly initially, yet the hidden expenses emerge when a business needs the software to align precisely with its unique processes. Customization involves modifying the software to meet specific needs, and this process can range from tweaking the user interface to integrating with existing enterprise systems. The degree of customization impacts the cost significantly as it requires skilled developers and a clear understanding of both the software and the business's needs.
Consider the potential challenges: software isn't a one-size-fits-all solution. Every business has its structure, demands, and peculiarities in their supply chains. The most effective software solutions will adapt to these unique requirements, but this customization comes at a price. For businesses in industries like pharmaceuticals or aerospace, where specific regulatory compliance is non-negotiable, the need for customized solutions becomes even more critical. This can lead to doubled or tripled expenses if not carefully planned and executed. When planning, it's important to account for the time and cost of initial customization as well as ongoing maintenance and updates, which should not be overlooked.
Integration, another crucial component, involves linking new software with existing systems. This is vital for businesses relying on multiple platforms for operations, from Customer Relationship Management (CRM) systems to Enterprise Resource Planning (ERP) solutions. The integration ensures smooth data flow, enhancing efficiency across the board. For example, a logistics company using a supply chain software must seamlessly integrate it with their current warehouse management system to avoid disruptions that could snowball into significant operational hiccups. A well-integrated system often requires consulting senior-level experts, which adds to the initial costs.
"Customization and integration are where supply chain software truly aligns with business goals, but doing it correctly is what separates the mediocre solutions from the exceptional," says James Carter, a supply chain technology consultant.
Factors affecting customization costs include the complexity of the supply chain, the level of existing system integration, and the need for bespoke reports or dashboards. Ensuring all stakeholders are involved in the process from the start can help mitigate risks associated with these challenges. This collaborative approach not only keeps the project within budget but also ensures the developed systems cater effectively to the requirements of all users, enhancing both adoption and satisfaction.
For those weighing these decisions, understanding customization and integration costs is as much about foresight as it is about current expenditure. Businesses must assess the potential Return on Investment (ROI) from day one. For instance, while the upfront costs could be substantial, the benefits such as reduced manual processes, improved accuracy, and enhanced agility can be significant game-changers in the long run, making the initial financial outlay worth every penny.
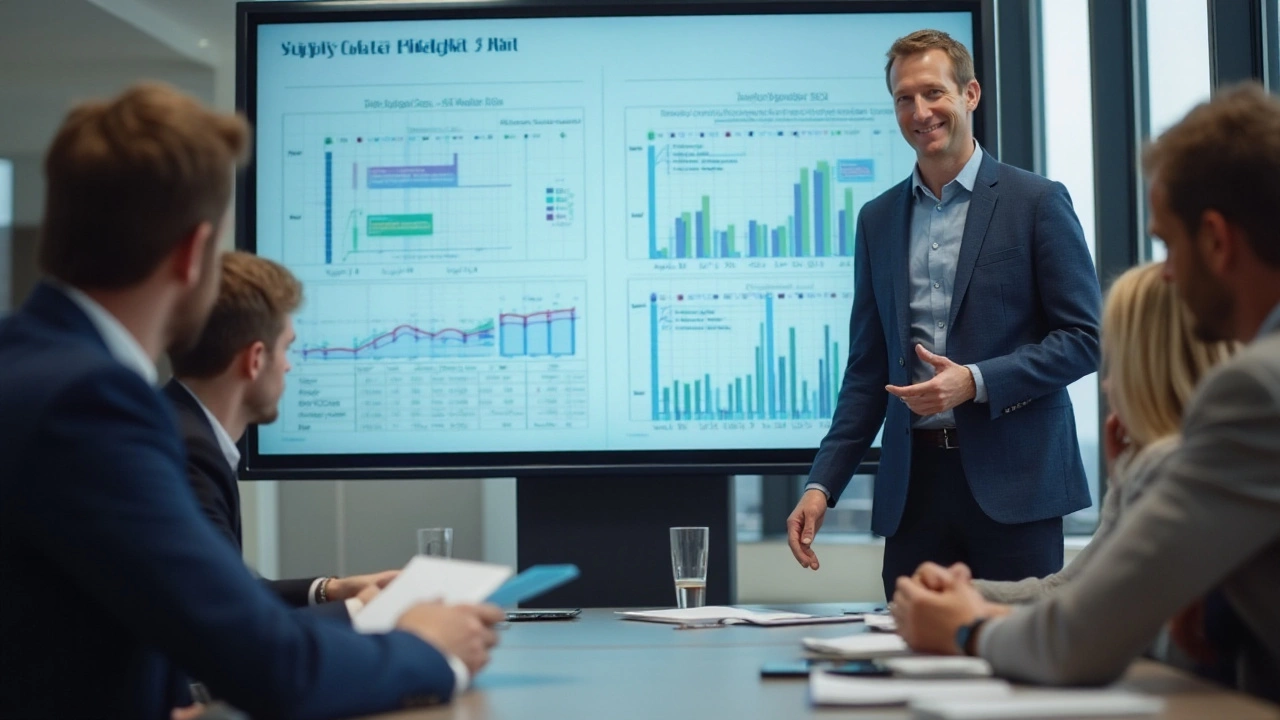
Evaluating ROI and Benefits
When it comes to investing in supply chain software, understanding the return on investment (ROI) and the accompanying benefits can provide businesses a valuable lens through which to assess their decisions. Calculating the ROI involves more than just tallying up immediate monetary gains. Instead, it requires a comprehensive look at both tangible and intangible perks that the software brings to the table. Financial gains might include reduced operational costs through enhanced efficiency, improved inventory management, and shortened lead times. By streamlining processes, companies notice a significant drop in errors and manual interventions, which often translates into time and cost savings.
The benefits of such software are not merely confined to monetary aspects. Tangibly, businesses might see an increase in customer satisfaction due to quicker response times and fewer order inaccuracies, which is paramount in a competitive market. A satisfied customer base often equates to increased loyalty and repeat business, which indirectly boosts the company's bottom line. Beyond the immediate financial evaluations, one should also consider long-term strategic advantages — such as scalability and agility — which are ingrained benefits of implementing sophisticated logistics software.
Measuring Success through Key Performance Indicators
In order to ensure that businesses are making the most strategic use of their supply chain tools, key performance indicators (KPIs) become essential. These can range from metrics like order accuracy rate and inventory turnover rates to customer satisfaction scores and service level agreements. By keeping a close watch on these, organizations can determine how effectively the software is meeting their operational goals. It's these metrics that inform a granular understanding of whether the software's implementation is yielding the expected improvements.
"Supply chain efficiency is no longer just about symbiotic relationships between costs and speed. It is about creating a seamless experience for the end user," explains industry expert John Doe from Supply Chain Innovations Magazine.
Table 1 below shows some common KPIs used in assessing the efficiency and success of supply chain solutions.
KPI | Description |
---|---|
Order Accuracy Rate | Percentage of orders without errors |
Inventory Turnover | Number of times inventory is sold/used in a given time period |
In conclusion, the benefits of supply chain software extend both directly and indirectly. By taking a holistic view of the ROI and beyond, companies are better positioned to justify the initial investment, recognizing the transformative potential of these tools in today's logistics landscape. Understanding and leveraging these tools can ultimately empower businesses to achieve not just improved efficiency but a stronger competitive edge in the market.