Ever wonder how online stores deliver your stuff so fast? It’s not magic—it’s all about the right warehouse solution. A warehouse solution isn’t just a place to stack boxes. It’s a set of tools and practices that keeps products moving smoothly from the moment they arrive, to the second they reach the customer.
If you run a business that stores products, picking the right setup can make or break your day. The right solution helps you track exactly what’s on the shelves, avoids lost items, and stops those moments where everyone’s scrambling to fix shipping mistakes. That’s why even smaller businesses are investing in smart warehouse solutions, not just giant companies.
You’ve probably heard about software systems that show you every item’s location or robots that fetch items faster than a person ever could. But a real solution goes further—bringing together tech, people, and even the layout of your warehouse. It’s meant to speed up the whole storage and shipping process, slash costs, and keep customers happy.
- Defining a Warehouse Solution
- How Warehouse Solutions Actually Work
- What Makes a Good Warehouse Solution?
- Common Tools and Tech You’ll Find
- Real-Life Perks for Businesses
- Getting Started With Your Own Solution
Defining a Warehouse Solution
If you picture a warehouse solution as just racks and forklifts, you’re missing the big picture. A real warehouse solution is the whole system that handles products from the minute they arrive until they head out the door. This includes the physical setup, the tech that tracks inventory, the team working in the space, and the rules for keeping things running tight.
One big part is inventory management. You need to know exactly how many items you’ve got, where each one is, and when you’ll run out. Without a proper solution, stuff gets lost, orders go out wrong, and restocking turns into a headache. With it, everyone’s on the same page, and your chances of a shipping mistake drop a lot.
A solid warehouse solution also sets up workflows—who does what and when. For example, the moment a pallet gets unloaded, it’s scanned and added to the system. Stock gets shelved in planned spots, and picking lists are generated by smart software. Even basic improvements, like better shelf labels or zones for fast-selling items, fall under this idea.
You’ll also hear talk of warehouse automation. That’s when machines or software do stuff people used to handle, like sorting, picking, or even driving forklifts. Real-life examples? Amazon’s robots shuffling shelves, or barcode scanners making sure the right item goes in the right box every time.
Old-School Storage | Modern Warehouse Solution |
---|---|
Manual paperwork | Digital tracking with software |
Items lost or forgotten | Real-time inventory counts |
People walk miles a day | Smarter layouts, automation |
Late or wrong orders | Picking accuracy over 99% |
The goal of any warehouse solution is simple: keep stock accurate, work quicker, spend less, and avoid headaches for you and your customers. That’s why businesses of every size are turning to smarter systems, even if they’re just starting out.
How Warehouse Solutions Actually Work
A warehouse solution isn’t just a single gadget or tool—it’s a whole system that ties everything together. Here’s what’s really happening behind those big doors.
First up, a solid inventory management system keeps tabs on every single item. As new products roll in, they get scanned and logged into a central database. That means at any moment, you know what’s in stock, where it sits, and when it needs restocking. If something’s missing or running low, you’ll spot it right away—less guesswork, more control.
Next, storage isn’t random. Warehouse layouts are planned so that high-demand items are easy to reach. Some companies use barcodes or even RFID tags, which makes picking and packing super fast. Pickers just scan a code and get clear directions right to the shelf. In warehouses with a lot of products, this shaves off a lot of time and confusion.
When it comes to moving products, automation plays a big role. Conveyor belts, robotic arms, and even driverless carts help shift heavy loads or repetitive orders. By the end of 2024, it was reported that over 40% of global warehouses used some form of automation, especially in large retailers and e-commerce hubs. Manual work still matters, but automation covers the dull or heavy lifting, leaving humans to solve problems and handle custom orders.
Step | What Happens |
---|---|
Receiving | Products arrive and get checked in, scanned into the system. |
Storing | Items are placed in specific spots based on demand and space. |
Picking | Orders are gathered using pick lists or handheld devices. |
Packing | Items are checked, packed, labeled, and made ready to ship. |
Shipping | Packages are sent out and tracking info is updated in the database. |
Finally, everything’s tracked by warehouse solution software. This isn’t just about inventory. The software connects the dots between incoming shipments, outgoing orders, and even team schedules. It spots slow-downs, bottlenecks, or mistakes way before they cost you money.
Thanks to all this, businesses get orders out faster, reduce mis-shipments, and avoid having shelves full of stuff nobody needs. It’s the kind of behind-the-scenes magic that keeps customers coming back for more.
What Makes a Good Warehouse Solution?
So what sets apart an average storage space from a great warehouse solution? It’s all about how easy it makes life for your business. The best setups keep things organized, fast, and simple, whether you’ve got a handful of shelves or a building the size of a football field.
First, a good warehouse solution gives you real-time visibility. A system that tracks every product the second it arrives (and leaves) keeps you from guessing what’s in stock. This means fewer headaches with lost items or angry customers calling because of inventory mix-ups.
Speed matters too. Your inventory management tools should help workers pick orders, pack them, and ship them out without wasted trips or confusion. The faster things move, the more orders you can handle—and the happier your customers are.
- Scalability: Can your system grow with you? If you suddenly double your product lines, a good solution won’t leave you stuck or scrambling to add new processes.
- Ease of Use: Nobody wants a system that requires a PhD to run. The best warehouse solutions are easy for your staff to pick up, with clear screens and logical steps.
- Automation Options: Whether it’s barcode scanners, picking robots, or automated conveyor belts, the more you can streamline boring, repeat tasks, the better. Studies have shown that smart automation can cut labor costs by up to 30% and reduce errors by almost half.
- Integration: Your warehouse solution should play nice with your supply chain software, shipping carriers, and even accounting tools. Everything works best when it all “talks” to each other.
Want proof all this matters? According to the latest industry research, businesses with an up-to-date warehouse solution ship 23% faster and see 50% fewer shipping errors than those running on pen-and-paper or clunky legacy tools.
Feature | Impact on Business |
---|---|
Real-time Inventory Tracking | Reduces stockouts and lost items |
Automation Tools | Lowers labor costs and speeds up order picking |
Easy Integration | Prevents double-entry and mistakes in orders |
Scalable Design | Grows with your business without extra hassle |
The bottom line: if your warehouse solution helps your team find, pack, and ship products with less hassle, you’re on the right path. Don’t settle for something that just keeps you afloat—aim for a setup that lets you outpace the competition.
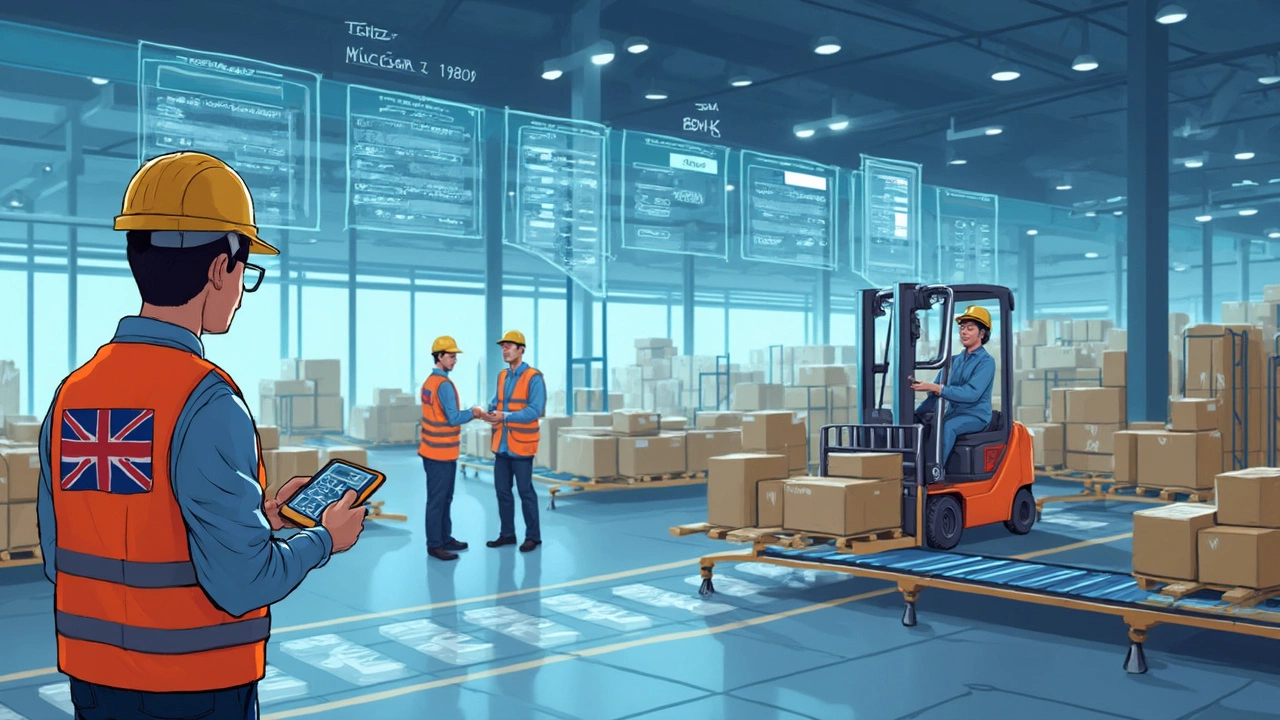
Common Tools and Tech You’ll Find
Every warehouse that runs smoothly has some standard gear and systems in play. The most popular piece? Warehouse Management Software (WMS). This is like the brain of the whole operation. A solid WMS lets you track inventory in real-time, see what's coming in or out, and avoid the painful stockout or double-order mess.
But that's just the start. Here’s what you’ll run into in most places using a real warehouse solution:
- Barcode Scanners and Mobile Devices: These gadgets cut down on errors. Staff scan items when they arrive, move, or ship out. Everything updates instantly, so you’re not stuck with manual spreadsheets.
- Automated Storage and Retrieval Systems (AS/RS): Fancy name, but the idea is simple: machines bring the product to the picker, not the other way around. This saves a bunch of walking and speeds things up when you’re filling orders.
- Conveyor Belts and Sorters: These move goods across the warehouse and can sort packages by size, route, or even shipping carrier. For high-volume operations, these save hours every day.
- Inventory Management Tools: Besides the main WMS, many warehouses use mobile apps or add-on features to watch stock levels, flag low inventory, or sync with sales platforms.
- Robotics: Think robots zooming around picking and delivering products. Big names like Amazon and Walmart use hundreds of these to boost speed and keep costs down.
Stacking all this tech together leads to serious productivity jumps. According to a 2024 study, adding just a barcode system and WMS can cut picking mistakes by 67% and speed up inbound receiving by more than 30%.
Tool or Tech | Main Benefit |
---|---|
Warehouse Management Software | Live inventory visibility, fewer errors |
Barcode Scanners | Speed and accuracy for item tracking |
AS/RS | Reduces walking, faster picking |
Conveyor Belts | Quick movement of goods |
Robotics | Automation, lower labor costs |
All these tools can work together. The key is picking what matches your warehouse size, product type, and budget. When everything clicks, you’ll see fewer mistakes, faster orders, and less stress for everyone on the floor.
Real-Life Perks for Businesses
Investing in the right warehouse solution can seriously pay off. Here’s what actually happens for businesses that ditch the spreadsheet shuffle and level up their warehouse game with tech and better systems.
First up, the speed factor. Modern warehouse solutions let teams process orders much faster. For example, a study done by Warehousing Education and Research Council found that companies using automated picking systems sped up order processing by up to 40%. No more customers waiting forever or getting the wrong box sent to their doorstep.
Accuracy takes a massive jump, too. Barcode scanning alone can cut picking errors by over 60%. That means fewer returns, less time spent fixing goof-ups, and happier repeat buyers.
Here are other big wins:
- Better inventory management: You know what’s in stock, what’s running low, and what’s collecting dust without staring at a clipboard for hours.
- Cost savings: Lower error rates and faster processing mean you need less overtime and can get by with a smaller crew, especially during busy seasons.
- Scalability: When your orders spike, your systems handle the heat. You won’t have to panic-hire or scramble around looking for extra space.
- Safety improvements: Automated paths and smart layouts mean fewer accidents and workers hauling heavy stuff less often.
If you’re into numbers, check out this breakdown of what businesses report after rolling out warehouse management software:
Metric | Before Solution | After Solution |
---|---|---|
Order Accuracy | ~85% | 98%+ |
Inventory Errors per Month | 20+ | <5 |
Order Processing Time | 24 hours | 8 hours |
Annual Labor Cost | $400,000 | $300,000 |
When you put all of this together, it’s clear that picking the right warehouse solution isn’t just nice to have. It can change everything—from your costs to your customer’s happiness and your sanity during peak times.
Getting Started With Your Own Solution
Diving into a new warehouse solution isn’t as tricky as it might sound, but there’s a lot more to it than buying racks and calling it a day. The first thing you need is a clear idea of what your business really needs–not just today, but for the future too.
Start by looking at your current operation. Ask yourself: What always slows us down? Where do mistakes keep happening? Do we run out of space or lose track of what’s in stock? Write down the pain points. This list is way more helpful than just guessing because most warehouse headaches are totally fixable with the right approach.
Next, set up a simple plan:
- List your top goals. (Quicker picking? Less running around? Fewer shipping errors?)
- Map out your inventory flow—from receiving goods to shipping them out.
- Check what tech you already use. Basic spreadsheets? Old barcode scanners? Fancy warehouse management software (WMS)? Figure out what needs an upgrade.
- Talk to your team. They often spot issues managers miss, since they’re on the ground using the system every day.
When it comes to choosing tools, don’t rush. A solid warehouse solution these days almost always includes a WMS to keep tabs on stock levels, manage orders, and even handle returns. The best systems work with your other business software, so you don’t have to re-type info or fix mistakes by hand.
Let’s put some numbers to it. According to a 2023 survey from Peerless Research Group, nearly 79% of warehouses using a modern management system reported up to 25% faster order picking speeds. That means customers get their stuff quicker, and you cut back on overtime headaches for your staff.
Tool | What It Fixes | Estimated Benefit |
---|---|---|
WMS Software | Locates products instantly | Reduces lost items by up to 35% |
Barcode Scanners | Speeds up stock checks | Slashes inventory errors |
Automated Conveyors | Moves orders faster | Boosts picking efficiency |
Here’s a tip: don’t try everything at once. Start simple—add a WMS or upgrade your scanners—and see what works before tossing in robots or conveyor belts. Keep training regular. Even the best tools won’t fix things if no one knows how to use them right.
Once you put your plan in play, keep checking results. Track shipments, returns, mistakes, and picking times. Make changes when stuff slows down—or when your business starts to outgrow the current setup.