Imagine a world where every part of a warehouse runs like a well-oiled machine; that's what a Warehouse Management System (WMS) aims to achieve. For businesses handling logistics and inventory, the significance of a WMS can hardly be understated. It's more than just software—consider it the backbone of smooth warehouse operations.
With the digital age making its mark, the traditional methods of managing inventory are evolving, and WMS solutions are at the forefront of this change. These systems don't just keep track of goods; they improve efficiency by streamlining operations and making sure that everything, from receiving to shipping, is done right the first time.
Whether you're new to the concept or looking to deepen your understanding, exploring the world of warehouse management systems reveals not only how they work but also how they can transform your logistics game. Let's dive into the nuts and bolts of WMS and explore why it's becoming a necessity in modern-day warehouses.
- Introduction to Warehouse Management Systems
- Key Features and Benefits of WMS
- Implementing a WMS: Tips and Best Practices
- Future Trends in Warehouse Management Systems
Introduction to Warehouse Management Systems
The concept of a Warehouse Management System (WMS) is quite fascinating when you think about how it's revolutionized bulky and sometimes chaotic warehouse environments. In essence, a WMS is software designed to optimize warehouse operations, focusing primarily on the movement and storage of inventory within a warehouse and related transactions, including shipping and receiving. It's no longer sufficient to simply know what's on the shelf; modern supply chains demand real-time information and efficiency. This need for immediacy and accuracy is what a WMS provides, acting as a digital heartbeat to help manage inventory.
This type of system ensures that inventory data is updated continuously, enabling businesses to react swiftly to changes in customer demand or supply chain disruptions. The idea is to achieve precision and flexibility, ensuring that every item is accounted for and easy to find. Notoriously, mistakes in warehouse management can lead to significant financial losses. According to the logistics experts at McKinsey, optimizing a warehouse with a robust WMS can reduce operating costs by up to 20%. Such systems are indispensable where fast-paced logistics demand not just accuracy but speed.
The rise of e-commerce and globalization has increased the demand for more sophisticated warehouse solutions. A WMS contributes significantly to customer satisfaction by ensuring timely delivery of products and reducing the chances of stockouts or overstocking. But it's not just about software; it's an integration of systems that work together, involving people, processes, and technology. Implementing a WMS involves a careful look at all operational aspects, right from the space utilization to the picking processes and beyond.
"A WMS is not just a service; it's a strategy. It's how you create value within your logistics strategy." — Logistics Expert, Rosemary Beals
While the benefits are clear, understanding how such systems are structured is crucial. Typically, these systems offer functionalities such as tracking inventory levels, order processing, and replenishment strategies. With inventory control at its core, a well-implemented WMS aids in the effective management of every piece of information regarding the items housed within a warehouse. It helps ensure inventory is accurate and that the right products are picked and shipped on time. Adapting to a WMS often means recalibrating existing warehousing processes, which brings challenges but also invaluable improvements in the long run.
The Evolution of WMS
As businesses have grown and become more complex, warehouse solutions have evolved from being simple inventory control systems to comprehensive management systems. Initially, warehouses relied heavily on paper-based systems which, albeit functional, were imperfect. With the advent of technology, digital solutions emerged, providing the accuracy and efficiency lacking before. Modern WMS solutions now integrate with other systems like ERP (Enterprise Resource Planning) and TMS (Transportation Management Systems) to provide an end-to-end view of an entire supply chain. This cross-system integration ensures that each department in a company, from sales to customer support, has access to accurate, updated data.
Today's WMS platforms also use advanced technologies, including AI and machine learning, to predict demand trends and optimize stock levels. Such advancements have brought a significant increase in warehouse productivity, and given the unpredictable nature of business, having agile and adaptive warehouse solutions is critical. The decision to implement a WMS involves an analysis of current deficiencies and future needs, translating these into a strategic advantage for any forward-thinking company. Each organization must tailor its WMS according to its specific operational needs to maximize its benefits.
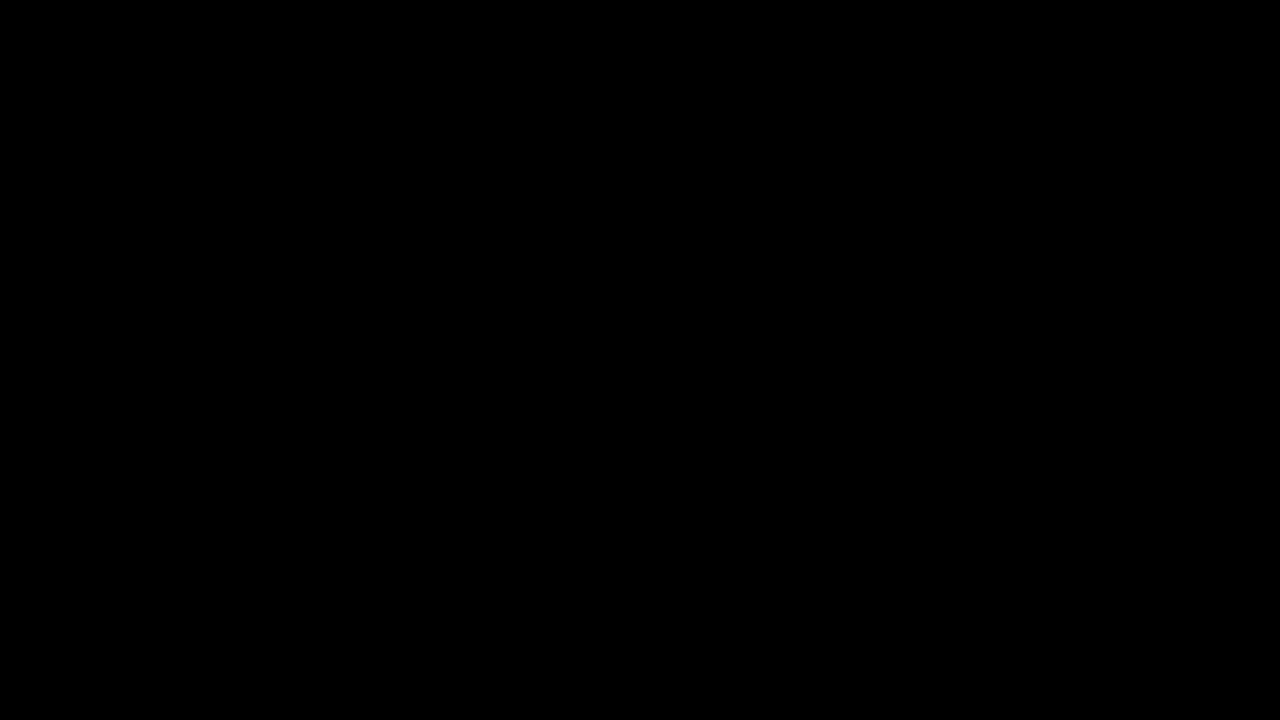
Key Features and Benefits of WMS
Warehouse Management Systems are at the heart of modern supply chain operations, serving as the epicenter where myriad tasks converge and synchronize. Among the first things to appreciate about a Warehouse Management System is its ability to optimize inventory management. By providing real-time updates, a WMS allows for precise tracking of stock levels, minimizing surplus and inventory loss. It’s like having an eagle’s eye view on every product that enters and exits the warehouse, ensuring that nothing slips through the cracks unnoticed.
Another standout feature of WMS is its role in labor management. By automating routine tasks, these systems free up human resources, allowing employees to engage in more complex problem-solving activities, effectively boosting productivity. Through task interleaving, a WMS can even assign multiple tasks in a way that maximizes efficiency while minimizing downtime. It's akin to orchestrating a symphony where every instrument knows precisely when to play, all contributing to the harmony of the warehouse.
An effective WMS also excels in order fulfillment, which is crucial for maintaining customer satisfaction. By streamlining processes such as picking, packing, and shipping, these systems ensure that orders are completed accurately and swiftly. This not only reduces shipping errors but also enhances customer experience, leading to repeat business and customer loyalty. A strong inventory control mechanism further fortifies this benefit by ensuring that the right products are always available for fulfillment.
"A proper WMS implementation can reduce operating expenses by up to 30%," notes a report by the Logistics Bureau.
Space optimization is another hallmark of a sophisticated WMS. By intelligently managing warehouse space, these systems maximize storage capabilities without the need for additional square footage. They achieve this through strategic placement of goods, considering factors such as size, weight, and turnover rate. The result is a more organized warehouse that operates efficiently without wasting valuable space, much like a game of Tetris played to perfection.
Finally, the importance of seamless data integration cannot be overstated. Modern WMS solutions often come with advanced reporting tools that provide insights into every facet of warehouse operations. These insights can drive data-driven decision-making, enabling businesses to refine processes continuously. Integration with other systems such as Enterprise Resource Planning (ERP) further extends the capabilities of a logistics ecosystem, creating a cohesive flow of information across various operational aspects.
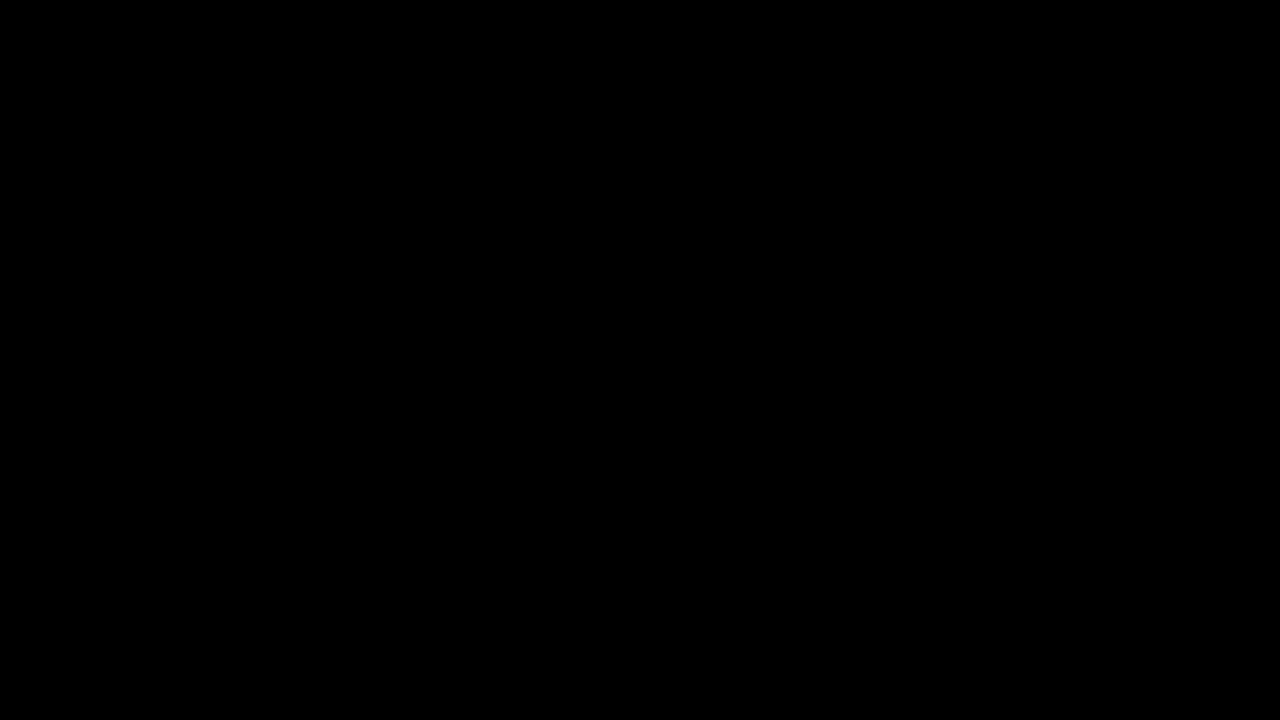
Implementing a WMS: Tips and Best Practices
Embarking on the journey to implement a Warehouse Management System (WMS) can be a game-changer for your logistics and supply chain operations. However, like all significant changes, it requires a structured approach to ensure a smooth transition and successful integration. The first critical step is to perform a comprehensive analysis of your current warehouse processes. Understanding the specific needs and pain points of your operations is crucial. This involves gathering input from all stakeholders, including inventory managers, warehouse staff, and IT departments, to get a holistic view of what your business truly requires from a WMS. Consider factors such as the scale of operations, types of inventory handled, and the complexity of processes when assessing potential systems.
When choosing the right WMS, ensure it aligns not only with your current needs but also with future growth potential. The most effective WMS solutions are scalable and flexible, allowing for system upgrades and expansions without disrupting other business functionalities. Investing in a robust system that supports both cloud-based and on-premise models can offer flexibility and resilience against unexpected challenges. Another best practice during the implementation phase is to create a phased rollout plan. This involves gradually transitioning various warehouse functions to the new system. By adopting an incremental approach, your team can adapt to changes more comfortably, and any unforeseen issues can be identified and addressed without hampering the entire warehouse operation.
Training is another vital component of successful WMS implementation. Equipping your staff with the necessary skills and knowledge enables them to use the new system effectively. This means providing tailored training sessions that cover everything from basic operation to advanced features of the WMS. An ongoing support structure with regular training updates as new features roll out ensures your team stays current with the system’s capabilities. Additionally, fostering a culture that encourages feedback can help identify training gaps and improve adoption rates. Regarding system integration, ensure that the WMS is compatible with your existing software, such as Enterprise Resource Planning (ERP) systems or Customer Relationship Management (CRM) tools, to facilitate smooth data flow across all platforms, enhancing overall efficiency.
According to Gartner, companies that optimize their WMS implementations see up to a 25% improvement in warehouse productivity.
Monitoring and measuring performance post-implementation is also key to refining the system for optimum utility. Regularly review Key Performance Indicators (KPIs) to assess the WMS's impact on inventory accuracy, order fulfillment rates, and labor productivity. Data-driven insights can reveal areas requiring improvement or adjustments, ultimately leading to enhanced effectiveness and efficiency. A culture of continuous improvement, supported by technology that evolves with your business, fosters innovation and competitive advantage. Finally, be open to feedback and solicit suggestions for improvement from the team members who interact with the system daily. This ensures the WMS remains a dynamic tool, evolving in line with the ever-changing demands of the logistics landscape.
Implementation of a strong WMS might initially seem daunting, but with meticulous planning and execution, it's a transformative process that pays off. By focusing on clear objectives, facilitating stakeholder collaboration, and prioritizing training and support, businesses can significantly enhance their warehouse operations, paving the way for improved inventory control and streamlined logistics.
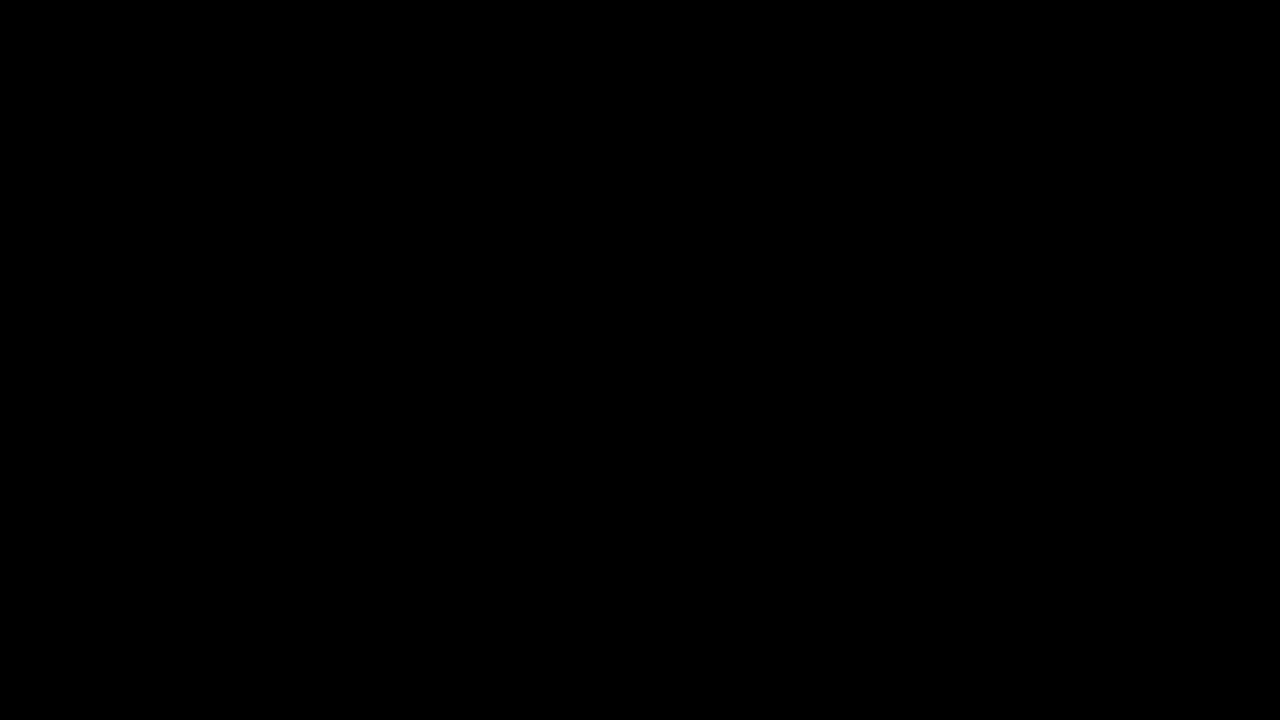
Future Trends in Warehouse Management Systems
The world of warehouse management systems is continuously evolving, driven by technological advancements and an ever-increasing demand for efficiency. As we look to the future, several trends are anticipated to reshape how warehouses operate and manage inventory. One notable trend is the integration of artificial intelligence (AI) and machine learning into WMS solutions. These technologies are not just buzzwords; they are transforming the landscape by enabling predictive analytics, automated decision-making, and enhanced operational insights. For instance, AI can predict demand patterns, allowing businesses to adjust inventory levels proactively, thus minimizing excessive stock or out-of-stock situations. This predictive capability is helping many companies reduce costs and improve service levels.
Another significant trend is the growing role of automation and robotics in warehouse operations. The adoption of autonomous robots for tasks such as picking, packing, and sorting is becoming prevalent. These robots work alongside humans, increasing the efficiency and accuracy of warehouse operations. By reducing manual errors, automation helps improve overall productivity. The rise of self-navigating robots, which can optimize routes inside warehouses, further exemplifies how automation is reshaping logistics. According to a recent industry report, the global robotics market is expected to reach $42 billion by 2025, driven largely by demand from the logistics sector.
Cloud-based WMS deployments are another trend gaining considerable momentum. As companies seek scalability, flexibility, and cost-reduction, the cloud offers a compelling solution. With cloud-based systems, businesses can easily scale their operations without significant infrastructure investments. Moreover, they offer better data security and accessibility, as well as seamless integration with other business systems. A study by Gartner indicates that by 2025, more than 90% of new large supply chain deployments will be cloud-based, a significant increase from previous years. This shift reflects a growing confidence in cloud technology and its benefits.
"The switch to cloud-based WMS solutions allows for more agile responses to the changing business landscape. It's an enabler for innovation and real-time data sharing," says Susan White, a renowned logistics analyst.
Finally, sustainability is becoming a critical factor in WMS trends. Businesses are increasingly aware of their environmental footprint, and as a result, eco-friendly practices are being integrated into warehouse operations. This includes optimizing delivery routes to cut down on fuel consumption, using renewable energy sources within facilities, and implementing recycling programs. Moreover, the concept of a 'green warehouse' is gradually taking hold, where sustainable practices are prioritized and measured. Embracing sustainability not only aligns with global environmental goals but also improves brand reputation and customer loyalty.
Future WMS will need to be adaptable, integrating seamlessly with various technologies and accommodating the rapid growth in e-commerce and global logistics networks. As companies strive to remain competitive, the onus will be on embracing these trends to drive efficiency and sustainability. By staying ahead of these developments, businesses can transform their warehouses into smarter, more responsive environments that meet the demands of a dynamic market.