In the bustling world of e-commerce, getting goods from warehouse to doorstep isn't as straightforward as it seems. The art and science behind it can be encapsulated by the 4 P's of logistics—Product, Process, People, and Performance. Each of these pillars plays a unique role in the dance of logistics.
So why are these 4 P's so essential? They are the blueprint of an efficient supply chain, ensuring that products are not only delivered on time but also meet customer expectations. Understanding these can give businesses the edge they need in a highly competitive market.
As e-commerce continues to grow, the logistics industry must adapt quickly. This requires an understanding of the finer details of each 'P' and how it can be leveraged for better operational success. Join us as we dive into these critical components and explore their impact on the world of online retail.
- Defining the Product
- Streamlining the Process
- Empowering the People
- Measuring the Performance
- Integrating Technology
- Adapting to Market Changes
Defining the Product
In the intricate web of e-commerce logistics, 'Product' stands as the cornerstone of the entire operation. It all starts with the goods themselves. The nature of the items being shipped can influence almost every logistical decision, from storage solutions to transport choices. Think about how varying dimensions, weight, and fragility of items require different handling procedures and packaging materials. Understanding the nuances of each product category is critical for any business looking to streamline its operations. For instance, a company that specializes in apparel will have different logistical needs compared to a tech company shipping delicate electronics. Both need to decide on appropriate packaging that minimizes waste while maximizing protection and customer satisfaction.
Determining the nature and specifications of the product isn't just a matter of logistics planning. It has direct implications on cost efficiency and environmental impact as well. Let's be honest, a lightweight, compact item is going to be cheaper and eco-friendlier to ship than a bulky, heavy one. This in itself can influence strategic decisions made at the product development stage. Simple adaptations in design can lead to significant logistical benefits. According to insights shared by industry experts,
"A well-defined product strategy in logistics can save companies up to 15% in shipping costs and significantly reduce carbon footprints."These strategic choices aren't just for cost-savings but contribute to an overall sustainable model that appeals to the environmentally-conscious modern consumer.
The importance of clearly defining and understanding your product extends beyond just size and shape; it also encompasses understanding demand and customer expectations. Data analytics plays a key role here. With numerous online tools available today, businesses can predict trends and prepare their logistics to meet upcoming demands. This includes having enough stock on hand and planning for any potential supply chain disruptions. During holiday seasons, for example, the increase in volume can drastically affect logistics strategies. How the product is perceived, packaged, and received by the customer can also feed back into brand reputation, so it's critical to align logistics considerations with marketing and customer service teams as well. To drive success, collaboration among all these departments is essential.
Streamlining the Process
In the realm of e-commerce logistics, streamlining the process is akin to crafting a symphony where each note must hit at the right time. The key to achieving this harmony lies in understanding the series of steps that define the journey from order placement to delivery. This process begins the moment a customer clicks 'buy', triggering what is known as order fulfillment. At this stage, the responsibilities are not solely to pack and ship but also to update stock levels and manage expectations regarding delivery times. Efficient processing at this step is crucial for customer satisfaction and retention.
But how do businesses ensure efficiency? Technology serves as the backbone of modern logistics. Warehousing management systems (WMS) and transportation management systems (TMS) are vital tools that optimize inventory handling and route calculations respectively. Many successful businesses implement automated picking and packing methods, employing robots to handle repetitive tasks with precision. Additionally, real-time data analytics offer insights into process bottlenecks, allowing for timely interventions. However, technological investments should align with the specific needs of the business to avoid overly complex systems that hinder rather than help.
The environmental dimension is another vital aspect of streamlining. Sustainable practices such as eco-friendly packaging and carbon footprint reduction are imperative in today’s logistics. By adopting green alternatives, businesses not only meet regulatory requirements but also appeal to environmentally conscious consumers. Many giants in the industry now track emissions and adjust their supply chains accordingly. An old maxim puts it well, "Efficiency is doing things right; effectiveness is doing the right things," and it echoes through the green strategies implemented to streamline operations.
Another crucial element in enhancing the process is communication. Establishing an open line between departments involved in logistics—sales, inventory management, and shipping—demands a level of coordination that is often underestimated. Communication breakdowns can lead to errors in orders and delays in shipping schedules, both of which negatively impact customer perception. Companies that prioritize seamless communication protocols often employ integrated communication systems to provide real-time updates, reducing human error. A strong communication framework is not just about relaying information; it's about ensuring clarity and reducing ambiguities that might disrupt the logistics flow.
And then there is the unique challenge of scalability in logistics processes. As e-commerce businesses grow, logistics must adapt to handle increased volumes without compromising service quality. The approach to scalability must be forward-thinking, integrating flexible strategies that anticipate future growth. Seasonal spikes in demand, like those during holiday periods, test the limits of logistic processes. To meet these demands, businesses often rely on temporary workforce boosts and flexible shipping arrangements. But flexibility alone is not enough; predictive analytics play a critical role, allowing businesses to forecast demand and prepare for it proactively.
Managing returns, often dubbed reverse logistics, completes the process cycle, and its optimization is a crucial part of streamlining. A smooth returns process enhances customer trust and satisfaction. Companies invest in developing customer-friendly return policies that are easy to understand and execute. Efficient management systems handle returns swiftly, ensuring products are processed back into inventory, repaired, or recycled as needed. While it might seem like an afterthought, the importance of a robust return system cannot be overstated—it is a significant differentiator in customer experience.
The process of streamlining logistics reflects a confluence of technology, sustainability, communication, scalability, and return management. Each element is a piece of a larger puzzle, and when placed correctly, it creates an efficient, customer-centric logistic operation. As someone wisely said, "Logistics isn't about goods moving to consumers, it's about consumers moving to the goods they want," a notion that epitomizes the essence of a streamlined process.
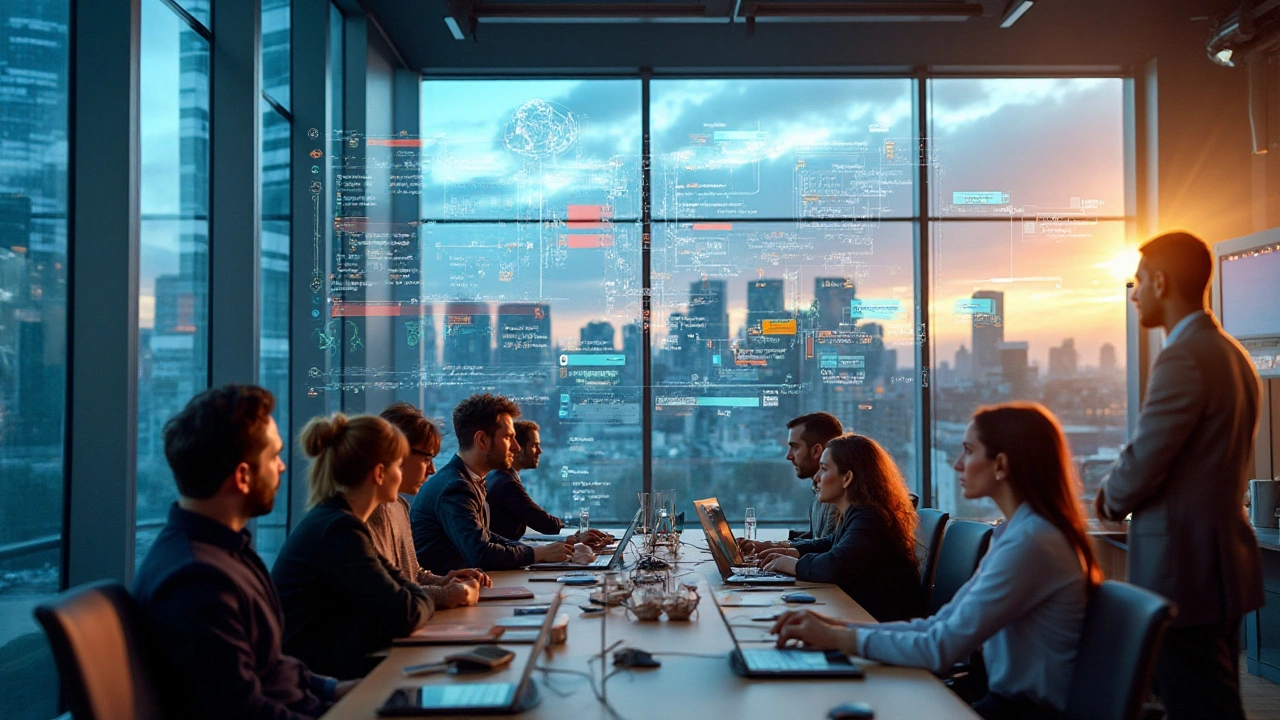
Empowering the People
In the realm of logistics, even the most advanced technology and streamlined processes would be nothing without the dedicated individuals driving them. The human element is the backbone of any successful e-commerce operation, and empowering the workforce is both a necessity and an art. By fostering a culture of growth and development, companies can unlock their hidden potential and drive efficiency to new heights.
Training and continuous education are key components of empowering people in logistics. As the industry evolves with technological advancements, keeping the workforce updated with the latest knowledge ensures that they remain competitive and capable. Workshops, online courses, and hands-on training sessions are invaluable resources that provide staff with essential skills and adapt to new challenges. It's about creating a learning environment where curiosity and innovation are encouraged, leading to a more motivated team with a shared goal of operational excellence.
Another crucial aspect is leadership. Managers and team leaders play a pivotal role in setting the tone for company culture. They must be approachable, empathetic, and lead by example. By providing clear communication and setting attainable targets, leaders can foster an atmosphere of mutual respect and trust. Regular feedback sessions and open-door policies enable employees to voice their opinions and contribute ideas, making them feel valued and integral to the company’s success.
"The greatest leader is not necessarily the one who does the greatest things. He is the one that gets the people to do the greatest things." - Ronald Reagan
Encouraging collaboration among teams is also essential. When people from different departments work together towards common logistic goals, it can lead to innovative solutions that a single team might overlook. Cross-training staff can also be beneficial, allowing them to gain insight into different functions and fostering a more cohesive, flexible workforce. This type of integration not only strengthens the company’s operations but also aligns employees with the broader vision of the business.
Recognizing and rewarding achievements goes a long way in empowering people. Incentives, both financial and non-financial, can motivate the workforce to strive for excellence. Awards for exceptional service, innovative ideas, or performance benchmarks create a sense of accomplishment and drive competition. Celebrating these milestones fosters a sense of community and belonging, which can translate into higher retention rates and a more committed team. By nurturing their people, companies don't just enhance their supply chain; they build a resilient, adaptable team ready to face the ever-changing landscape of e-commerce logistics.
Measuring the Performance
When it comes to logistics, measuring performance isn't simply about counting packages. It's about understanding how each cog in the machinery contributes to the greater whole. In the realm of e-commerce, this understanding is key to providing timely and reliable service. An effective way to gauge performance is by utilizing a combination of Key Performance Indicators (KPIs) such as shipping accuracy, order cycle time, and lead time variability. Start by identifying these metrics and tracking them meticulously. It's like setting benchmarks in a race, giving you a clear view of where you stand and where improvements can be made.
Monitoring these metrics not only provides insights but also helps to show trends that may have been overlooked. Creating a detailed dashboard for all stakeholders ensures that everyone stays informed and aligned on goals. For instance, achieving a high order fill rate should be every e-commerce logistics team’s dream. This ensures that products available in stock are shipped without fail whenever an order is placed. According to a recent report, companies that keep their order fill rate above 95% are likely to see a significant increase in customer retention. Maintaining this figure requires seamless coordination between the warehouse and transportation management systems.
Revisiting performance regularly can help identify areas in need of improvement. Implementing quarterly performance reviews ensures that no stone is left unturned. Employing these processes could lead to efficient cycles and evoke a forward-thinking culture within logistics. As logistics guru Alan McKinnon once said, "Measuring logistics performance is like conducting an orchestra; every section must harmonize to create the perfect melody."
Where one chain is weak, the whole is affected. An overwhelming majority of logistics failings can be traced back to easily addressable issues in performance metrics.
Technological integration plays a role as well, automating the processes of measurement through sophisticated software which can track how well the supply chain is performing. Real-time data helps in making informed decisions and adjustments on the fly. For those skeptical about data integration, it's worth noting that companies investing in data-driven logistics see up to a 10-20% decrease in operational costs. This approach provides a dynamic way of adapting and responding to unexpected challenges in the swiftly changing world of e-commerce.
KPI | Target Value |
---|---|
Order Fill Rate | > 95% |
Delivery On-Time | > 98% |
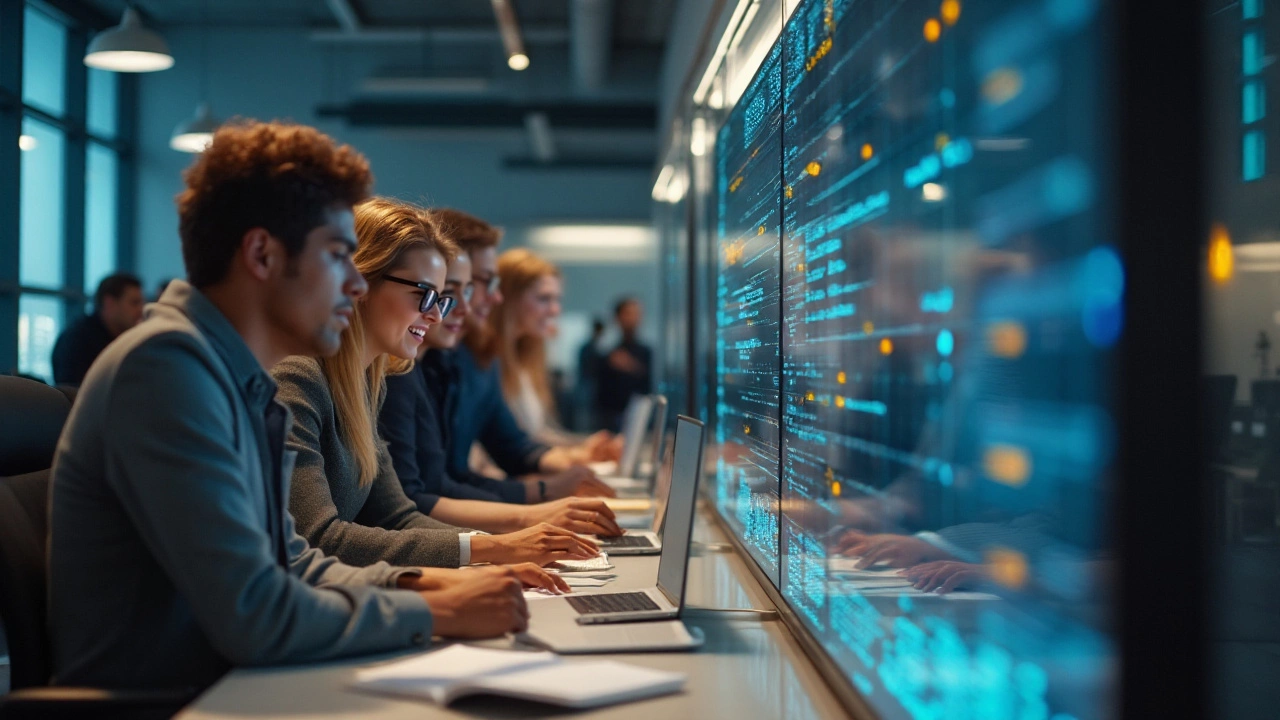
Integrating Technology
In the realm of e-commerce logistics, technology is the catalyst that transforms ordinary processes into seamless operations. The advent of cutting-edge innovations such as Artificial Intelligence (AI), the Internet of Things (IoT), and blockchain has revolutionized how logistics firms conduct business. These technologies provide real-time data and analytics, aiding in predictive analytics that preemptively tackles issues before they escalate. With AI's power, companies can optimize delivery routes, minimize delivery times, and significantly cut down on fuel consumption, leading to both economic and environmental benefits.
The implementation of IoT devices plays a pivotal role in logistics by ensuring that all data is interconnected and easily accessible. IoT sensors are often used in warehouses to monitor conditions like temperature and humidity, assuring that products, especially those sensitive to environmental conditions, are stored optimally. The capability of tracking inventory in real-time reduces human error and increases inventory accuracy, enhancing the reliability of logistics operations. As a result, businesses are less prone to stockouts or overstocking, which are common issues that can disrupt the supply chain.
Blockchain technology, with its decentralized ledger system, brings transparency and security to logistics transactions. This is particularly crucial for supply chain management, as it allows every stakeholder to access verified, immutable transaction records. This level of transparency not only boosts trust among parties involved but also expedites processes that traditionally required manual verification. It can reduce disputes and payment delays, leading to smoother financial operations across a company’s logistics network. A remarkable aspect of blockchain is its potential to prevent counterfeiting, a significant concern in the e-commerce landscape.
"Blockchain not only enhances security across transactions but also introduces a level of traceability that was previously unheard of," says supply chain expert A.P. Green. "This change is what e-commerce vendors need to prevent losses and increase customer trust."
Robotic automation in warehouses, another technological breakthrough, reshapes logistics by handling repeated and mundane tasks, freeing up human resources to focus on more critical operations. Robots ensure that order picking is faster and error-free, which directly correlates with customer satisfaction. Automation also opens doors to 24/7 operations without the fatigue factors that human workers face, making logistics more efficient and reliable.
Finally, with the rise of augmented reality (AR) and virtual reality (VR), training logistics staff becomes more interactive and effective. AR can offer real-time assistance to warehouse employees, showing paths to products or crucial operational information. VR can create immersive training scenarios, mimicking actual tasks employees will encounter, reducing the training time significantly and preparing the workforce for complex situations.
Altogether, integrating these technologies not only enhances the existing logistical frameworks but also prepares businesses for future disruptions and demands. The key takeaway for e-commerce platforms is to invest in such tech-savvy solutions, as they hold the power to propel operational efficiency and customer satisfaction forward, both hallmarks of a successful logistics strategy.
Adapting to Market Changes
In the ever-evolving realm of e-commerce logistics, staying ahead of market changes is not just advantageous—it's essential. The digital marketplace is in a constant state of flux, driven by consumers' changing preferences and technological advancements. E-commerce platforms need to be agile, adapting their logistics strategies quickly to survive and thrive in such an environment. A crucial aspect here involves recognizing trends, such as the increasing demand for sustainability and personalized shopping experiences, and shaping logistics practices accordingly.
One of the key areas where adaptation is evident is in delivery expectations. Over the years, the bar has been raised significantly, with next-day or even same-day delivery becoming the norm rather than the exception. It's not just about speed; it's about precision and reliability, ensuring that the right product arrives at the right time. From a logistics perspective, this requires a robust network of warehouses and distribution centers strategically located to minimize delivery times while optimizing costs. Companies like Amazon are continually expanding their fulfillment centers, fine-tuning routes, and experimenting with drones and autonomous vehicles to meet and exceed customer expectations.
Logistics providers must also grapple with external pressures such as global events and economic shifts affecting the supply chain. Take, for instance, the impact of the COVID-19 pandemic. This unprecedented situation forced companies to pivot and rethink their logistics strategies almost overnight. Many learned that having a flexible supply chain, capable of quickly adjusting to supply-demand fluctuations, was pivotal in maintaining service levels. According to a report by McKinsey, companies that had digitally transformed their logistics showed higher resilience and adaptability during such global disruptions.
"The future of logistics must be digital, and businesses have to adopt technology to not only keep up but stay ahead," noted Sarah Jones, a logistics technology expert at the Global Supply Chain Summit in 2023.
Another critical component in adapting logistic operations is technology integration. This goes beyond simple automation; it encompasses the adoption of AI, machine learning, and predictive analytics to anticipate market changes before they happen. For example, advanced data analytics can predict future demand patterns, enabling more accurate inventory and resource planning. This predictive capability helps in eliminating waste, reducing costs, and ensuring that businesses can scale rapidly when needed.
As enticing as new technology sounds, businesses must evaluate their current logistics strategies and infrastructure. A practical approach is to conduct a comprehensive audit of existing processes, identifying areas that need technological intervention. During this phase, engaging with software specialists and logistics consultants can provide insights into the most effective solutions tailored for specific business needs. It’s not just about adopting technology for technology’s sake, but rather integrating solutions that streamline operations and enhance customer experience.
Business leaders should remain vigilant, tuning in to shifts in consumer behavior, technological breakthroughs, and industry trends. Creating dynamic logistics models that can be easily modified according to both anticipated and unforeseen changes will provide a competitive edge. As the digital economy continues to mature, those who can deftly navigate the waters of change, leveraging technology and innovation without losing sight of fundamental logistics principles, will emerge as the frontrunners in the e-commerce landscape.